Master's Project: TAB B CAT
Toxic Algae Bloom Buster Clay Aquatic Treatment

During the Spring of 2024, I designed, built, and tested my master's project: a robot which combats harmful algal blooms (HAB) using clay flocculation.
​
Clay has been used for decades to fight HAB. The clay particles combine with the algae and sink, killing the toxic organisms, which need sunlight to survive. My robot mixes clay into water to create a slurry and then can spray this mixture onto algae blooms.


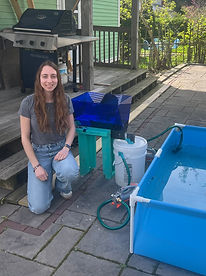

Above is the poster I presented during the ME Poster Presentation. The PDF can be found here.
Final Presention
The project is officially finished! During the past two weeks I:
-
Tested the auger system with a new, faster motor which allows for a better clay ratio.
-
Tested the clay samples I received from WHOI, and the auger system moved them with no problem.
-
Cut holes for the hoses and secured them to the bucket.
-
Tested the pump's speed.
-
Spray painted the wood structure and secured the electronics to it.
-
Tested the whole system at once.
-
Finished all the calculations.

The auger pushed clay out at a rate of ~4.5 grams/second. The pumps moved the slurry at a rate of ~3.5 gallons/minute.
The slurry was sprayed out at a consistency of ~20 grams/Liters, compared to the WHOI standard of 20-30 grams/Liter
All in all, the system was a successful proof of concept for a portable system which can create and disperse clay slurry for HAB management. It can hold 40 pounds of clay, which is enough to treat half to a full acre of affected water, and it mixes the slurry to an acceptable consistency of 20 grams/Liter. The system cost approximately $300, with the two pumps being the biggest expense.
The current product is a prototype, and it requires further development to improve its overall appearance, durability, and robustness. The size and form can also be easily adjusted, which may be needed depending on the use.
​
Videos can be found in the above section!
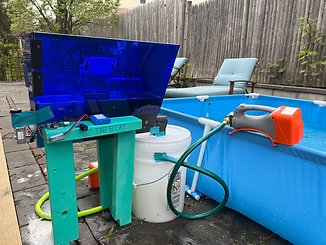

Meeting 5: 4/16/2024

There are only two weeks left before my poster presentation! Before our meeting, I worked to get a pump working. I failed to fix the first one, so I ordered the same one again. When that one had the same defect, I ordered a different one. This one worked! And it has normal hose attachments for input and output, which is much better. I put a hole in the side of the bucket and in its lid and I created a crude support for the auger system out of spare wood in the school makerspace.
I set the system up outside and ran it with the lid off so that I could see what was happening inside. It was a success. I ran the input pump until the bucket was partly full, then turned on the output pump. Then, I turned on the auger system. When the hose was pointed straight forward, it did a pretty good job of mixing the slurry together. The output hose was at the bottom of the bucket, so by the time the slurry was at the bottom of the bucket, it was very mixed. The output of the pump has a wide spray pattern, so I decided to utilize this rather than needing to use a hose with a sprayer. When the system was turned off, it could be seen that clay had been dispersed pretty evenly. I am unsure how to check the exact amount of clay in the slurry, though.
​
A video of this working can be seen here.
​
In the next two weeks, I need to finish the project! Here's everything that's left:
-
Test the auger when it is more full of clay (how well it works and how it changes the rate that clay leaves)
-
Add a hole in the bucket for the output hose
-
Secure the hoses
-
Create a structure which keeps the pumps, hoses, and motor secure and allows you to pick up and walk away with the system
-
Do calculations for the potency of the slurry and how much area the robot would be able to treat
Meeting 4: 4/2/2024
Before the fourth meeting, I began to manufacture and build. I first updated my CAD to only contain components that were small enough to be printed on my Prusa. I broke the screw and base into three pieces and I made the hopper a combination of printed PLA and laser-cut acrylic.

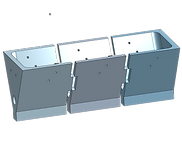.png)
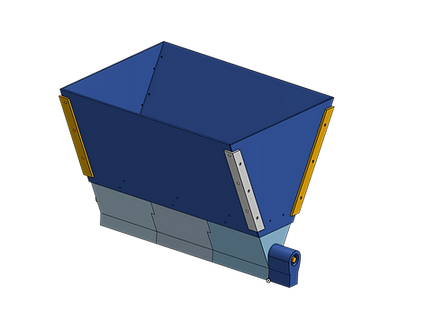


I put it together using heat-set inserts and bolts/nuts. I used superglue to keep the screw together in addition to the pegs that secure them.
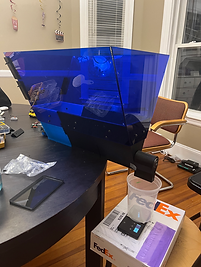

I then put a small amount of clay in the hopper (I still need to seal up the gaps before I can fill it) and turned the motor on. Success! Clay moves out at a rate dependent on the speed of the motor.
​
Next, I did a preliminary measure of how fast the clay is able to move out.
​
At its slowest, 5.63 grams of clay was dispersed over one minute (0.09383 grams/second).
At its fastest, 10.65 grams of clay was dispersed over ten seconds (1.065 grams/second).
​
Future investigation will see if the amount increases when the hopper is filled with clay. Once the rate of the pump is known, the proper amount of clay can be set. It is very possible I will need to get a faster motor.
​
See a video of one of my experiments here.
​
​
Before the meeting, I also worked on the pump. I built the kiddie pool that I had previously order and set up the pump. The pump comes with a filter for the input, which I will use for the pump that takes in the body of water, but which I will remove for the pump that takes in the clay slurry. The other end of the pump has a spray nozzle. I experimented with different spray patterns and found one that I think will work well for dispersing the clay. I will do more testing this in the future.
​
Unfortunately, the pump came with a leak at the output line. I ordered a barb pipe fitting to try to fix this.
​
Here are some videos from this week, including time lapses of me building, the spray pattern, and the screw auger.
​
During the meeting, I presented my progress and we discussed my remaining work.
​
Tasks for next meeting:
-
Fix pump or get another pump that works
-
Set up system and test whether the pumps are enough agitation to mix the clay slurry together
Meeting 3: 3/5/2024
Before the third meeting, I began ordering components. I bought a 50 lb bag of kaolinite clay, a kiddie pool, a hose, a bucket, and a Scotts Hand-Powered Spreader. I wanted to see if this off-the-shelf product could successfully spread the clay. Unfortunately, the clay proved too fine to work. When I added water to the clay it worked better, but still not reliable enough.
​
I did research on why this spreader wouldn't work, and I found that auger systems for fluidizable materials need to have large diameter screws with short pitches.

.png)
Example of screw for fluidizable materials
My CAD for the screw auger
I edited my CAD to fulfill this and made a smaller model of it, which I printed on my Prusa Mini+

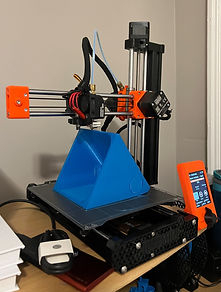
This was a success! The clay flowed out at a relatively constant rate with my hand-turning. Once I hook it up to a motor it should be even better.
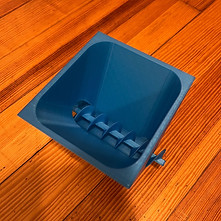
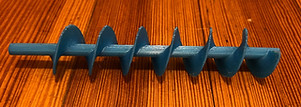

I also got in contact with Don Anderson, a senior scientist at Woods Hole Oceanographic Institution. I was able to get some exact answers for modified kaolinite clay:
-
For applying 10 g/m², they would use 20-30 grams of clay per liter in a stock solution.
-
Modified kaolinite has a median grain size (D50) of 23.5 µm. Normal kaolinite clay has a grain size between 25-35 µm, so it should work pretty well as a simulant.
-
This clay can treat multiple HABs, including red tide and cyanobacterial blooms.
Don also offered to send me a sample of modified kaolinite clay in order to test my robot! Once I get my auger system working, I will be taking him up on that.
​
​
I tried making a small batch of the stock solution just to see what I was working with. 20-30 grams of clay in 1000 grams of water is a very small amount. The batch turned out cloudy, but still flowed like water. Only a little bit of stirring was required to mix the clay into the water and it has still not completely settled two days later.
​
​And finally, I made an updated CAD model based on the new design, which will dump the clay into a bucket of water which will be pumped in, rather than pumping into a tube.
During our third meeting I gave an update on the last month and we discussed the new design. We decided that I would need to use two pumps: one for pumping water in and one for pumping slurry out.
​
Tasks for next meeting:
-
Order pump and experiment with it
-
Scale up and build auger system
-
Order auger motor and test it
-
Experimentally find the correlation between the motor speed and how much clay comes out
Meeting 2: 2/6/2024
Before our second meeting, I dove into researching clay for HAB. I read countless articles about various types of clay, its impacts on different types of algae, and its impact on water quality and animals. I quickly ran into a problem. All of the articles I was reading required a huge amount of clay for small areas: around 3,500 pounds per acre!
​
After hours of researching, it looked like I had to pivot with my design. I began brainstorming new options:
-
I could put a tank of slurry on land and pump it out to the robot on the water.
-
I could create an extremely scaled down product. It could work as a proof of concept for a larger product.
-
I could make a robot intended only for small ponds, such as the ones people maintain on their property.
-
I could choose a different method from clay.
​
After resigning myself to these new options, I stumbled upon an article about modified clays. These clays are mixed with polyaluminum chloride (PAC) and makes them much more effective against algae, and are needed at a quantity 50-100 times lower. Now that I would only need my robot to hold 35-85 pounds of clay, I pivoted back to my original plan and began CADing. I decided to make an auger system which would sprinkle dry clay into water being sprayed into the HAB.
.png)
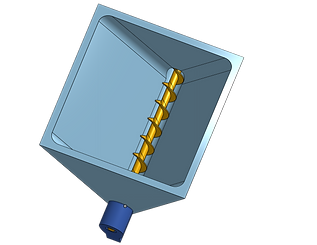.png)
During our second meeting, we looked over my rough CAD and I got feedback on my design. We talked about different methods of building the hopper in my auger system, such as sheet metal, plastic sheets, and 3D printing. We also discussed the components I should order.
​
Tasks for next meeting:
-
Order 50 lbs of clay
-
Find a play pool which is deep enough and big enough for testing
-
Order an existing auger system to try modifying
-
Order a powerful water pump
-
Find out the ratio of clay to water for the proper slurry
Meeting 1: 1/23/2024
Before our first meeting, I did research in various ways to combat HABs. I didn't want to spread toxic chemicals, so I ruled out those solutions quickly. I found that aerating the water had been found to kill algae. But in the end, I decided on clay. Clay has been found to have no negative impact on the environment and it is very effective.
​
I came to the meeting with several possible designs:
-
Screw conveyer/auger system which could sprinkle the dry clay into the water, possibly with a paddle in the water stirring it up.
-
Pre-make the slurry and spray it into the water with a nozzle and pump.
-
A rotating paddle wheel to disperse the clay.
-
Small holes in the bottom of the bucket which slowly release the slurry/clay.
​
I had prepared a list of goals for the project. With only a semester to work, Goal 1 is the priority and likely the only one that can be completed. However, the other goals are stretch goals there for if I have extra time.
-
Build a working system which disperses anti-algae material.
-
Build a working system which can move around a body of water.
-
Combine the two above systems.
-
Make the robot autonomous.
​
I also came with a general timeline. We discussed what needed to get done and decided that my goal for our next meeting would be to have a finished CAD and the meeting after that I would have my first round of components picked out and ordered.
​
Tasks for next meeting:
-
Create a CAD of my chosen design
-
Figure out how I am sourcing my clay
-
Figure out a testing location for the bot
-
Research whether the clay must be in a slurry or if it can be distributed dry
-
Research how much clay is needed
Before Meetings
After one of my previous classes got added to the list of approved electives for my master's degree, a free elective opened up for me. My advisor suggested that I pursue an individual master's project and I thought that would be a perfect way to end my time in school. I was excited by the idea of building any project I wanted and by the challenge of doing it independently, given that most of my projects so far had been group efforts.
​
I wanted to build an underwater robot and I wanted it to have a positive impact on the world. After a lot of brainstorming, I decided I would build a robot that would combat harmful algae blooms. They have been a huge problem in Massachusetts (and all over the world) lately, and I liked the idea of working on a local issue which could be scaled to a bigger picture.
​
I approached Matthew Woodward, my advanced robotics professor, and asked if he would be willing to be my project advisor. We had a meeting at the end of the fall semester and he agreed to mentor me and meet with me every other week in the spring.